History of the Railroad Article 10
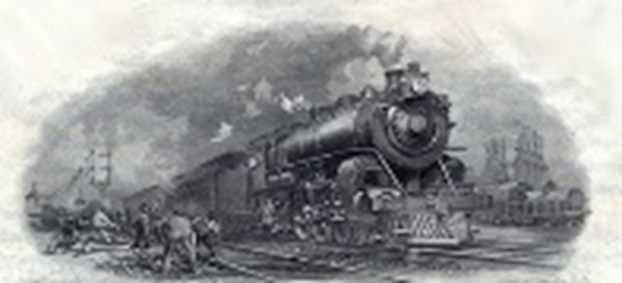
The Building of the Railroad
Laying Track Part 1
The railroad was one of the single greatest developments of the modern age. You might say the highway was linking cities, towns and states. Maybe space travel was a greater development? I might say the invention of Pepsi was, it has been my favorite choice since I bought my first one at Ernest Ruth’s store in Knob Lick in 1962.
Building any railroad system was an arduous task. After the surveying crew had laid out the route to take, the tie gang, played a vital role in its construction.
Before we get to much further into this article, we need to tell the story of how we got the wooden tie. Yes, there is a story behind the wooden tie. There always is a story behind everything.
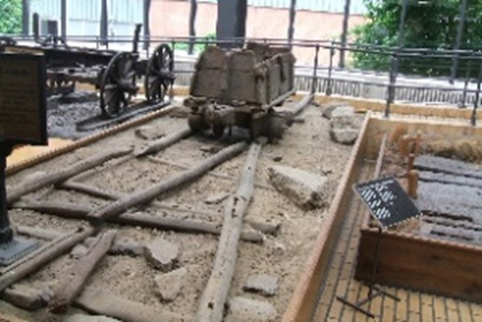
Afterbrunel, Public domain, via Wikimedia Commons
The above picture is of a section of track from the 16th century gold mine in Transylvania. The wooden wheels, which had a pronounced flange, guided the wagon along. The rails were made of crude logs, made out of small trees, placed atop cross ties.1 Today you would almost laugh at it, but back in the day it was the “Bees Knees.” Wrong era, but you get the drift.
In the last article we saw how the steel rail was born. It has not always been a fact that the steel rails sat upon wooden cross ties as we know it. In the birth of the modern-day railroad, stone blocks were used to place the cross ties to support the steel rails.
Robert Stevens, the president and chief engineer of the Camden and Amboy Railroad of New Jersey, were laying track and ran out of stones upon which to lay the rails on. Desperation is a mother of invention. So, needing an alternative material to use, Stevens came up with ties hewn from logs. The forest close to where they were laying track had an abundant supply of trees which they could use for the purpose needed.
After they had laid the track, then riding the rails where wooden ties were used, Stevens noticed that the wooden cross ties offered a smoother ride.
The wooden ties were called sleepers. They secured the track firmly and helped provide a stable base. Thus, the smoother ride.
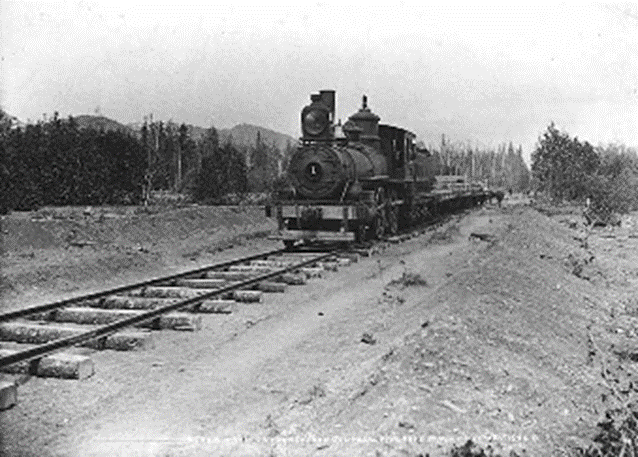
Tails On Rough Cut Logs, No Ballast
University of Washington, Public domain, via Wikimedia Commons
The ties primary material of choice is hardwood. Oak is the number one sought after material. It offers the strength needed along with longevity. 2 Another reason hardwood was ideal was if it could firmly hold spikes in place.
The railroad relied on getting ties to keep construction progressing. Missouri was the ideal place to contract for them. The hardwoods needed were indigenous to the area, plus their abundance made it the ideal place.
In the 1800’s, as the railroad pushed westward, a continuous supply of ties was needed.
Missouri’s forests were strategically located and were brimming with the sought-after hardwood, such as oak.
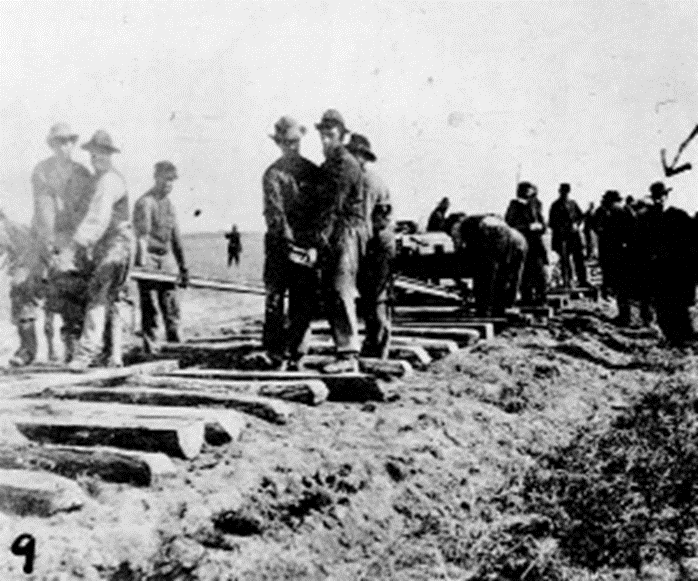
Men Laying Rails On Roughly Cut Rails
Public Domain, Wiki Commons
Men called Tie Hackers would search in the forest, looking for a tree that would yield ties that would pass inspection.
Their tools consisted of a two-man crosscut saw, a double bit axe, a broad axe, and a measuring device called a tree scantling to ensure the correct length. Then they had a mule for getting the logs to the river where they would tie them together for transport down river. Then a small quantity of coal oil for removing resin and gum from their saw blades.
They would enter the forest for a full day's work. Packing a lard bucket filled with a mason jar containing drinking water and covered in toe sack to keep the water cooled. Plus, it carried their lunch of beans, fried pork, cornbread, and an onion.
For a full day's work, a good tie hacker could produce 10 to 15 ties daily.
The railroads were specific in the dimensions. Also, if there was even a knothole, this would cause the tie to fail inspection and be worthless.
Some hackers found a way around this. They would cut out the knot and insert a dowel of the same material in the hole. They would use a broad axe to scrape it was smooth and then rub some dirt on the area to help hide their deception.
The ties would be cut to 8 to 10 inches square and 8 to 10 feet in length, depending on their application.
In the 1930s, the tie hacks would receive 50 cents a tie. They would receive on average $5 to $6 per day for a standard 12-hour work shift. The landowners seem to have gotten the short end of the deal. In the early days the landowner received no monetary compensation. It wasn't until the mid-1930’s, when the price of ties increased, that the landowner received about 25 cents per tie.
Again, the number of ties that were required were ever increasing. In 1900, 110 million ties were needed annually. These were untreated ties which had a life expectancy of four to six years.
Creosote, a coal tar, was started to be used as a preservative. This increased the ties life expectancy to be about 30 years. 3
Meanwhile, back at the track. Tie gangs laid the sleepers (ties) and steel rails on the roadbed. To fully capture the true job of the tie gang, here is a step-by-step process they followed. Sidetracks were filled with supply trains. Each would be carrying tons of steel rail. Also loaded on the cars with thousands of cut ties.
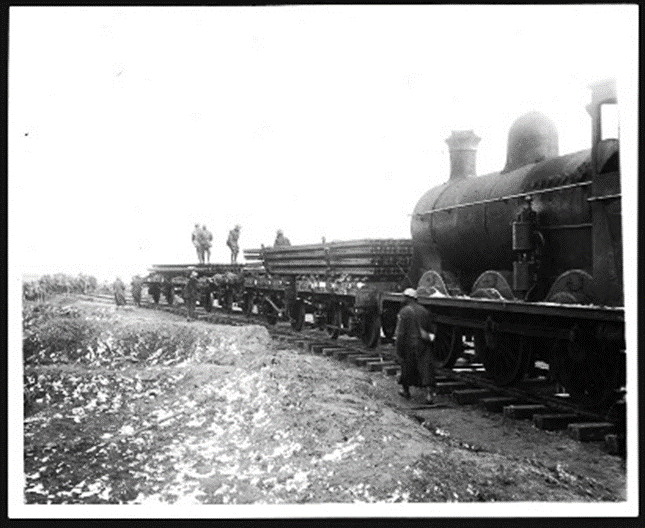
Supply Train Loaded With Rails
No Known restrictions Wikki Commons
Horse and wagon brought the rails, ties, spikes, and fish plates. Men would quickly unload the wagons and send them back for more.
The ties would be placed upon the roadbed laid 19 to 19 ½ inched apart or 3,250 wooden ties per mile.
Five men on both sides would seize the rail with their tongs and start forward. They came at a run placing them on the ties on the roadbed. Then came a demand of “Down.” You would hear the command shouted about every 30 seconds.
The gauger would set his measuring rod, which is exactly 4 feet 8 inches and 1/2 inches, the standard gauge and measure the correct width between the rails. After the rail was checked the chief spiker and his men would make their hammers sing out. Two rails every 30 seconds were laid down, and four rails a minute. Listening to the steady beat of the sledgehammer.
There would be thirty men driving spikes, three strokes per spike, ten spikes per rail. Four hundred rails per mile. 3
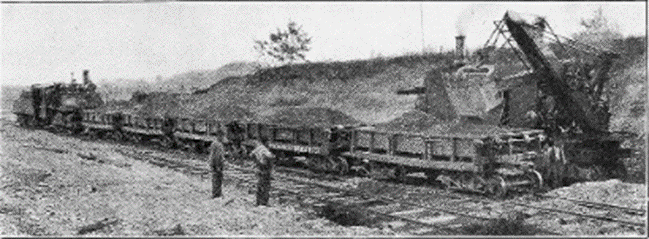
Scooping Ballast for Transport
Public Domain, Wiki Commons
Ballast is the last item applied and another vital part of the roadbed. It not only keeps moisture drained away to keep the roadbed solid but is a support base for the ties and rails. It gives strength and rigidity to hold up to the stringent force exerted by the passing train. It also makes it have a flexibility to help absorb the energy induced when the train passes over it.
Over time, it has been found that limestone and quartz make the best ballast. It is a hard stone, and it will lock together, strengthening the base even more. 5
The ballast needs to be packed down and at least the depth should be up even to the height of the tie. The ballast also needs to be extended out 14 inches on either side of the track sloping downward for drainage.
If the system that was just described had been constructed properly, there would be no standing water on the track or in the ditches running parallel to the track. There also would not be any foliage growing in the draining ditch.
There is maintenance required. The ballast would require washing to allow the water to run away from the roadbed. Plus, there would be times when the sleepers would need replacement.
Most people can identify some parts of the railroad. The spike is the most recognizable. The spike is so simple, that most people can draw it. Even if you don't possess the drawer’s gene. I don't know if there is one, but if there is, I don't possess it. So, I’ll show you a picture. Although simple looking, it took a while to perfect. In the beginning of the modern railroad, there was nothing to compare it to.
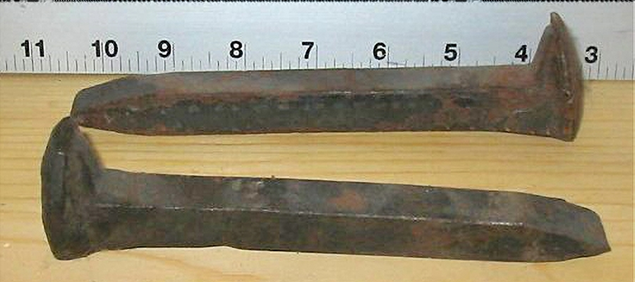
Railroad Spike
Creative Commons Attributions Share Alike 2.0
Photo by Sean Adams